Engineered Bamboo: The Truth About Formaldehyde, Water, and Resins
There is a lot of misinformation being spread about bamboo, from its reputation for running wild, to the toxic resins used in the production of engineered bamboo and its unsuitability as a building material.
Here we will try and debunk some of these myths.
Bamboo is uncontrollable
Bamboos are giant grasses with woody stems that spread by underground rhizomes. They are hardy and grow on most soils and are relatively pest and disease free. There are two distinct types of bamboo which are defined by the way they grow – running or clumping. Bamboo is native to all parts of the world except Antarctica and Lapland. While there are over 1,700 species only 90 have been documented for use in construction.

Clumping bamboos expand slowly around the edges during each annual growth cycle, producing stems that grow underground only a short distance from the parent plant. They may spread from 5 to 30cm in a season. Running bamboos extend their rhizomes by vigorously sending out underground stems that grow rapidly from the parent plant before producing vertical stems. They may grow from 10cm to 1m in a growing season.
Whether you are growing bamboo in a plantation or a garden, regular maintenance is essential. Proper maintenance consists of regularly removing dead canes, clearing out dead leaves and culm sheaths and properly watering so the bamboo doesn’t dry out and die. Controlling the spread of the rhizome (particularly in running bamboo) should also be considered and can be as simple as a preventative barrier, or removal of the additional rhizome. This is a very similar process to preventing grass from invading garden beds.



Thick-walled bamboo (Dendrocalamus asper) and bamboo pole construction example
The best bamboo species for building and construction are generally found in the tropics, as they grow taller and bigger than temperate bamboos and have thicker walls which result in better structural and mechanical properties. For construction purposes, wall thickness, density and fiber strength are the most important properties for greatest structural strength. Giant bamboos with thick walls are best for heavy duty construction, whereas smaller diameter bamboos or large bamboos with thinner walls are suited for lighter structures, and engineered products.
Misinformation

Japanese knotweed, often referred to as Japanese bamboo (Fallopia japonica knotweed) is a rhizomatous member of the knotweed family that is aggressive in its growth and spread. This is a noxious, invasive species that crowds along roadsides and waterways, affecting ecosystems by pushing out native plants and limiting plant and animal species diversity. With origins in Japan and East Asia, they were introduced as ornamentals in the late 1800s and have unfairly contributed to the misconception that bamboo is uncontrollable.

But it’s not only Japanese knotweed that gets confused for something it is not. Victorian Ash is not an ash species but a eucalyptus species and Tasmanian Oak ís not an oak it is also a eucalyptus species. Radiata pine is identified as a significant environmental weed in Victoria and South Australia, and as an environmental weed in New South Wales, the ACT, Tasmania, Queensland and Western Australia. Source:
Quality
As with any product, the quality of base materials is always a factor in the quality of the end material. While bamboo reaches its full height in its first growing season and the tensile strength remains the same throughout the age of the bamboo plant, compressive strength increases as it gets older (5-6 years). While bamboo for packaging, textiles and paper can be harvested at 3-5 years, construction and engineered bamboo requires additional maturity to ensure the process of lignification is complete and is therefore harvested at 5-7 years.

So with the strength coming from the lignin it is important to harvest at a time suitable to the material you want to produce. Harvesting too early means the cell walls are softer and the resultant material will be of a much lower quality. While it will initally look the same as fully matured material, it will not have the durability of quality engineered bamboo. If you are looking at seemingly identical products and one is much cheaper than the other, then it is reasonable to assume, the base material was harvested before maturity.
Resin
Whether you are buying decking, floorboards, engineered timber or engineered bamboo, all of them utilise a bonding agent. Bamboo and timber tend to use the same bonding agent as the manufacting process is extremely similar.
Engineered products (strandwoven or laminated) are made by cutting the raw material (timber or bamboo) into strips and drying them. Strandwoven material then crushes these strips further before binding with a resin and compressing into a dense block. This material is generaly used for flooring, solid and multi-layer panels.
Laminated products stack 3-7 layers of dried lamellas at 90 degrees to the layer below, bonding the lamellas with adhesives before pressing to create a solid panel. Laminated materials can be either horizontal, vertical, or both and is used for flooring, beams, boards, wall panels, plywood, furniture and cabinetry.
So both processes use resin, but what type? Once again, this depends on the quality of the end product. Phenol formaldehyde (PF) is one of the most moisture-durable wood adhesive available and is also commonly used in the engineered bamboo industry. Urea formaldehyde is a cheaper alternative. Formaldehyde is a naturally occurring organic compound that exists in everything, including our breath and our cellular structure. Classified as a volatile organic compound (VOC), it is a chemical that becomes a gas at room temperature.
Phenolic compounds are phytochemicals found in most plant tissues, including cereals, coffee beans, fruits, vegetables, olives and tea leaves. The main groups of phenolic compounds include favonoids, phenolic acids, tannins, stilbenes and lignans.

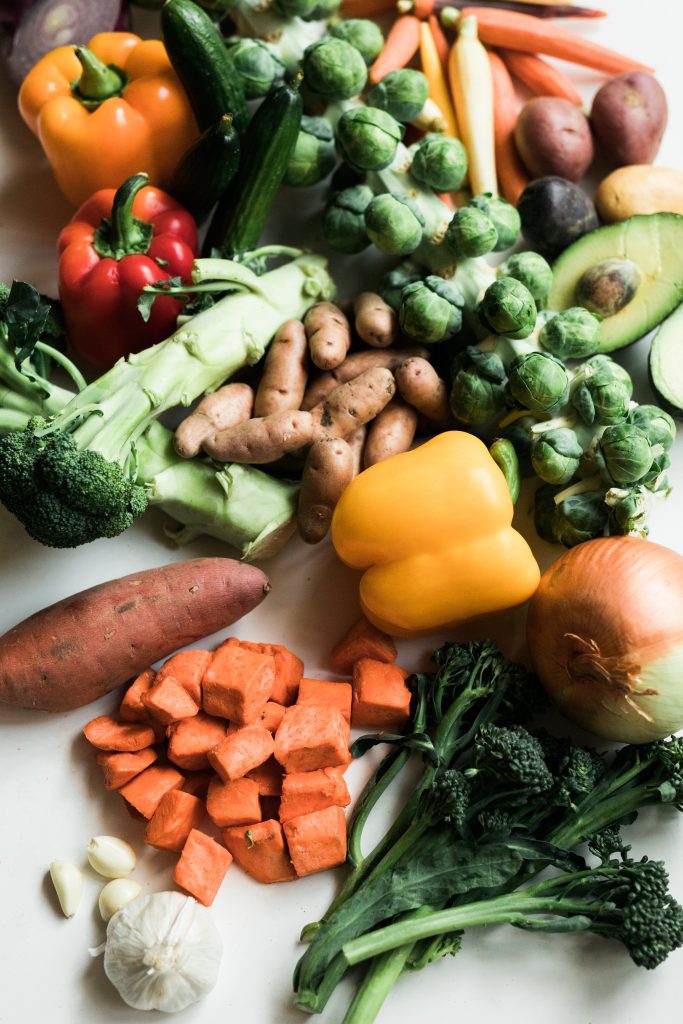




Urea formaldehyde (UF) and phenol formaldehyde (PF) are both high quality resins. Unfortunately, phenol formaldehyde has received a bad reputation because some early formulations contained toxic phenols. However, modern phenol formaldehyde resin is made from non-toxic phenols. Today, phenol formaldehyde is typically used without fear of toxicity while urea formaldehyde is followed by strict regulations to ensure low toxicity after curing.
Bamboo manufacturing adhesives emit 0.02ppm into atmosphere, below allowable amounts by all world standards, including Californian CARB Phase 1 and Phase 2, Japanese JIS/JAS, Australian Standard, U.S.OSHA, E0, and German emissions standard.
In comparison, formaldehyde is a common metabolic by product and occurs naturally in fruit at 58.3ppm, vegetables at 40.6 ppm, milk at 5.2 ppm.
Engineered bamboo emit less formaldehyde ppm than a banana, 1,500 times less and you will find more formaldehyde particles per million in coffee than in engineered bamboo. (Source World Health Organization.)
Low quality bamboo can contain traces of urea-formaldehyde. It is important to ensure you source materials from reputable manufacturers, preferably with eco-certifications.
Flooring

Have you heard that bamboo flooring:
- contains formaldehyde?
- expands and contracts excessively and is not suitable for dry or humid climates?
- is not as strong or durable as timber flooring?
Bamboo floring has been around since the 90s, but the original bamboo floors were not like today’s strand woven bamboo floors. Today, bamboo flooring is rapidly replacing traditional hardwood as a popular option in commercial and private applications.
In the 90s the technology and manufacturing processes were new and unsophisticated. But since then, the methods of manufacture have exploded with innovation leading to a variety of extremely high quality products. Deliberate misinformation in the early years about formaldehyde and bamboo flooring has inadvertently led to bamboo being one of the most tested and safe flooring products available today.
There are three types of bamboo flooring:
- horizontal bamboo floor where strips of bamboo are placed side by side and the nodes of the bamboo culm are clearly visible
- vertical bamboo floor where strips of bamboo are placed vertically and the appearance of the nodes is minimised
- strand woven bamboo flooring where bamboo fibers are compressed under extreme heat and pressure.

All three processes use bamboo harvested at 5-7 years to ensure the lignin strength of the bamboo is at its strongest. Strips are glued together with PF to create a board with a Janka hardness higher than traditional hardwood flooring.

Bamboo floors naturally expand and contract as the weather changes. You can minimise the amount that floors will swell and shrink during seasonal changes by keeping the humidity in your home within a 20% range. Humid climates are actually very suitable for bamboo flooring because they have relatively stable humidity year round.
Cupping will occur when there is moisture hitting the underside of the flooring, from the subfloor. Likewise when floorboards begin to ‘tee-pee’ it is usually a sign of excessive moisture under the boards – generally from water egress due to a leaking pipe or flooding. Confusingly, this ‘tee-pee’ often occurs at a distance from the original site of water egress, the boards expand and push subsequent boards until there is no movement left and two boards ‘pop’.
The great majority of gapping, cupping and ‘tee-pee’ is a result of sub par installation, or environmental factors, not defective product.
Once again, the quality of your bamboo floor will depend on the reputation of the bamboo manufacturer or retailer. The maturity of the harvest, type of resin and manufacturing process all play a part in the cost of your floor, by buying a cheaper product you may save on the cost, but you could well be sacrificing on quality.
Features | Bamboo Flooring | Hardwood Flooring |
Hardness(resistance to denting) | 10 | 7 |
Eco-Friendliness | 10 | 6 |
Indoor Air Quality(off gassing/toxicity) | 10 | 10 |
Warm & Cozy Underfoot | 10 | 10 |
Water-Resistance | 8 | 7 |
Price | 9 | 6 |
Natural Material(not synthetic/plastic) | 10 | 10 |
Natural Look & Feel(no repeating patterns) | 10 | 10 |
Ease of Installation | 9 | 9 |
Ease of Maintenance | 8 | 8 |
Facts

- Bamboo should be harvested at 3-7 years (depending on end use)
- Engineered bamboo contains less formaldehyde ppm than your daily coffee
- Bamboo lacks volatile oils and has a high silica and water content, so it is much harder to ignite than timber. It can be used to quickly replenish damaged landscapes after fire, flood, earthquake or other disasters.
- Construction grade bamboo has an average tensile strength around 160 N/mm2 which is 3 times higher than most conventional construction grade timbers
- Construction grade bamboo has an average compressive strenth between 40-80 N/mm2 which is twice to four times the value of most timber species
- Construction grade bamboo has an averag bending strength between 50-150 N/mm2 and is twice as strong as most conventional structural timbers.
- You can plant bamboo and see the results in 5-7 years when the culms reach 30-40 feet. But you can’t witness the maturity of most trees in a lifetime.
We can educate the construction industry and public by myth busting the arguments against bamboo. From formaldehyde to suitability for flooring. The truth can be summed up by sending out a simple message to the new movers and shakers in the construction industry that the best time to plant a tree was 20 years ago and the best time to plant bamboo is now!
